
Gas Pipeline Constructure Service Overview
Gathering pipelines: move gas from production wells to gas processing facilities, which remove impurities such as sulphur, water, and carbon dioxide.
Feeder pipelines: transport gas from processing facilities to transmission pipelines.
Transmission pipelines are the major conduits of the pipeline network, transporting gas to markets, often across provincial or international boundaries.
Distribution pipelines deliver gas to residences, businesses, and various industries. Provincial regulators typically regulate these facilities.
Our range of services starts with the handling or commissioning of the detailed engineering in pipeline planning and extends to the entire construction including material procurement and installation up to commissioning.
What We Do
- Oil & Gas Pipeline Construction
- Aqueducts/Water Pipeline Construction
- Gas Utility Distribution Line Installation
- Pipeline Maintenace
- Pipeline Rehabilitation
- Hydrostatic Testing

Pipeline Construction
we are young with experienced staffs and partners. we are anxious to grow and be one of the best pipeline construction companies in the field. Our company is fully equipped and qualified to complete any mainline pipeline construction projects that keenly focused on the current midstream pipeline market, feeder pipeline, transmission pipeline, distribution pipeline, storage facilities. etc.
we are ready to complete your project, including new construction, relocation, replacement of existing pipe. etc. We will commit the resources necessary to make your project a success.
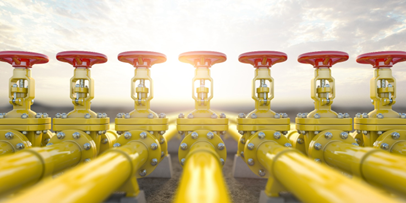
After all federal and state level permits are approved and all agreements are completed, the process of pipeline construction can be divided into the following steps/ procedures
step 1: Construction Staging Areas & Storage Yards
In order to construct a pipeline, staging areas and storage yards are cleared, strategically located along the planned right-of-way (ROW). These areas are used to stockpile pipe and to store fuel tanks, sand bags, silt fencing, stakes, and equipment parts, etc.
Step 2: Clear Cutting the ROW
After the equipment is accessible in the staging area, work will begin to clear cut the pipeline right-of-way.
Step 3: Excavating the Trench
The trench for the pipeline is dug after the ROW is cleared of trees.
Step 4: Pipe Transport, Stringing, & Assembly
When the trench is completed, pre-coated segments of pipe, usually 40 ft in length, are transported from stockpiles in the staging area to the right-of-way. Pipes are laid above ground beside the trench, or within the trench on top of supportive sandbags in steep terrain. Certain pipe sections are bent using a pipe bending tool to allow the pipeline to follow the planned route and the terrain. The pipe sections will then be welded together, sand blasted, and the weld joints coated with epoxy to prevent corrosion. Finally, the weld joints are inspected with x-ray to ensure their quality. Connected lengths of pipe can then be lowered into the trench
Step 5: Obstacles: Roads & Streams
At times, pipelines cross existing roads, highways, streams, rivers and wetlands etc. Each of these obstacles requires a unique method and order of operations.
Step 6: Testing & Restoration
After the pipe is inspected, the trench is filled in. Before completing the project, the pipeline integrity must be verified using hydrostatic testing. If the pipeline remains intact during this test, it is deemed operational. After this, the surface of the ROW is seeded and fertilized, and above-ground markers are placed along the pipeline path.

Additional Infrastructure
While the majority of a pipeline is underground, there are several types of supporting infrastructure that are constructed during a pipeline project. Compressor stations, facilities that maintain the pressure level within the pipeline, are built to support new pipeline projects, or existing stations are upgraded. Additionally, valve stations are built above the right-of-way along the pipeline, allowing operators to shut off sections of the line for maintenance or in an emergency. Metering stations are built along the length of pipelines, providing a measure of the flow of gas throughout the line.
To ensure pipeline integrity, welds must be x-rayed and the pipe hydro-tested. This process involves pumping in clean water, pressured above the expected MAOP — maximum average operating pressure. Then, all water is removed and “pigs” are inserted into the pipe to clean it out. When the pigs eventually exit the far end of the pipe clean, then the line will be filled with dry air. Air compressors pump up the air, and the air is run thru a drier. The air will be sampled and tested for moisture content. When those parameters get low enough, the complete pipeline is filled with nitrogen to absorb more of the remaining moisture. Only then is the pipeline ready to transport natural gas.
Pipeline Maintenance
The most important consideration in pipeline maintenance is safety, including operator safety, safety of the population and safety of the environment. Our commitment is to help our customers achieve pipiline integrity and zero incident
According to the Pipeline Association for Public Awareness, government statistics show that “a common cause of pipeline incidents is improper or unauthorized digging near a pipeline.”
Other major causes include “mechanical failure, human error, and corrosion.
The Pipiline Maintenance activity consists of the following
RIGHT-OF-WAY CLEARING
An important aspect of pipeline maintenance is right-of-way clearing. This is because a pipe needs a clear path of travel in order to operate the most efficiently and uninhibited.
During right-of-way clearing, trees and roots are removed so that the land near pipes is free of the threats of these conditions.
It’s also important that the right-of-way remains clear so that in the event of an emergency with your pipeline, it’s easily accessible for repair.
HYDROSTATIC TESTING
To ensure the strength of the pipes in a pipeline, hydrostatic testing is recommended before and during their use.
Hydrostatic testing is a procedure where the pipes you will use in your project are connected to one another. They are then filled with water at a higher rate of pressure than they will normally be.
These high pressures help you see how well your pipeline will perform under heavy use.
Besides doing this before pipes are put in the ground, hydrostatic testing is also used to measure the strength of pipelines over time.
IDENTIFYING CORROSION
A way to help extend the life of your pipeline is by monitoring your pipes for any evidence of corrosion.
Protecting your pipeline against corrosion begins long before your pipes are put in the ground. Depending on the material your pipes are made out of, you should ensure you’re using an anti-corrosive coating.
But even then, you still can’t protect 100 percent against corrosion.
This is because natural conditions and accidents create a threat to your pipes.
For example, a leak, emergency or natural disaster can cause serious damage. This means you should monitor how these substances impact your pipes.
One way to address corrosion concerns is to use “pigs”. These are devices used to identify corrosion. They also repair certain issues without losing production time.
MAINTAIN COMPLETE RECORDS
When it comes to maintaining your pipelines, you should keep accurate records.
By doing this, you’ll give others a complete record of the life cycle of your pipeline. Besides keeping a database of site plans and pipeline product guides, you should also take lots of pictures.
This helps when it comes to showing the condition of pipes at installation. It will also serve as an important baseline to determine how quickly your pipes are corroding.
PERFORM REGULAR INSPECTIONS